Sikafloor®-262 AS N
Epoxidharzbasierte, 2-komponentige, lösemittelfreie, ableitfähige Verlaufsbeschichtung für Gewerbe, Lager, Elektronik- und Pharmaindustrie.
- Elektrostatisch ableitfähig
- Gute chemische und mechanische Beständigkeit
- Flüssigkeitsdicht
- Dichte, seidenglänzende Oberfläche
- Rutschhemmende Strukturbeschichtung möglich
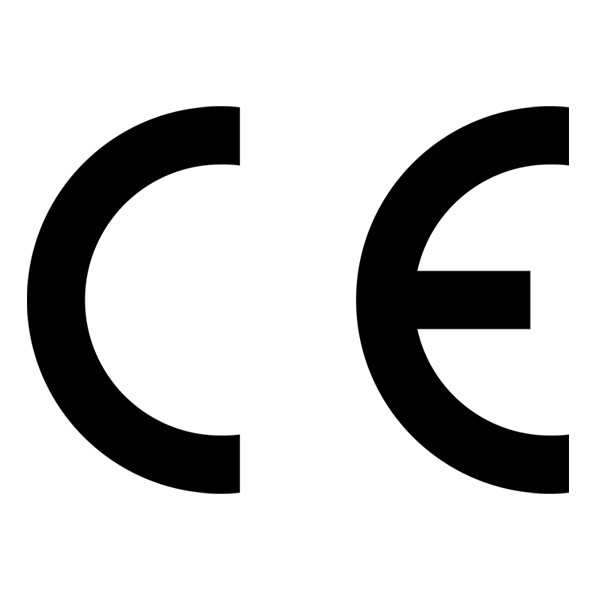
Anwendung
Zur Herstellung von selbstverlaufenden, farbigen, elektrostatisch ableitenden Epoxid-Beschichtungen auf Beton oder Zementestrich im Innenbereich. Einsatz in der Automobil-, Elektronik-, PharmaIndustrie, in Gewerbe-, Lager- und Ausstellungsbereich, Räumen mit Explosionsrisiko usw.Vorteile
- Elektrostatisch ableitfähig
- Gute chemische und mechanische Beständigkeit
- Flüssigkeitsdicht
- Dichte, seidenglänzende Oberfläche
- Rutschhemmende Strukturbeschichtung möglich
Verpackungseinheit
Komponente A | 21 kg Gebinde |
Komponente B | 4 kg Gebinde |
Komponenten A+B | 25 kg |
Farbe
Harz - Komponente A | farbig, flüssig |
Härter - Komponente B | transparent, flüssig |
Standardfarbton: RAL 7032, diverse Pastell- und Buntfarbtöne gem. Farbtabelle in aktueller Preisliste.
Alle Farbtöne sind ca.-Angaben da aufgrund der Kohlefasern, welche die Leitfähigkeit herstellen, der Farbton nicht exakte dargestellt wird. Geringe Farbtonabweichungen sind aus rohstoffbedingten Gründen unvermeidbar. Unter UV-/Witterungsbelastung sind Epoxidharze generell nicht farbtonstabil. Dies verändert jedoch die Produkteigenschaft nicht.
Produktdetails
UMWELTINFORMATIONEN
LEED Rating
Sikafloor®-262 AS N entspricht den Anforderungen an LEED EQ Credit 4.2: Gering emittierende Materialien: Anstriche & Beschichtungen SCAQMD Methode 304-91 VOC Gehalt < 100 g/l.
ZERTIFIKATE / PRÜFZEUGNISSE
- selbstverlaufende, farbige Epoxibeschichtung nach EN 1504-2: 2004 und EN 13813
- Brandprüfung nach EN 13501-1, Report-No. 2007-B-0181/17, MPA Dresden, Deutschland, Mai 2007
- Prüfung der elektrostatischen Eigenschaften nach IEC 61340, SP Institut, Test Report F900355:A, Februar 2009
- Prüfung der Verträglichkeit mit Lacken nach BMW-Standard 09-09-132-5, Polymer Institut, Test Report P 5541, August 2008
- Lackierbarkeitstest nach VW-Standard PV 3.10.7 (Farbbenetzungsmindernde Substanzen (PWIS)) wie Silikone, HQM GmbH, Test Report 09-09-132-4, 09.2009
- Emissionszertifikat Sikafloor®-262 AS N CSM Statement - ISO 14644-1, Klasse 4 - Report No. SI 1412-740, März 2015
- Ausgasungszertifikat Sikafloor®-262 AS N F CR: CSM Statement - ISO 14644-8, Klasse -8.0 - Report No. SI 1412-740, März 2015
- Widerstandsfähigkeit gegen Funkenflug UFGS-09 97 23 von Beschichtungssystemen, Test report P 8625-E, Kiwa Polymer Institut
| |
Zusammensetzung
Epoxy
Haltbarkeit
12 Monate ab Produktionsdatum
Lagerbedingungen
Trocken lagern in ungeöffneten und unbeschädigten Originalgebinden, bei Temperaturen zwischen +5°C und +30°C.
Dichte
Komponente A | ~ 1,69 kg/Liter |
Komponente B | ~ 1,03 kg/Liter |
Mischung | ~ 1,53 kg/Liter |
Gefülltes Harz 1 : 0,3 | ~ 1,69 kg/Liter |
Alle Werte bei +23°C
Festkörpergehalt (Gewicht)
~ 97 %
Festkörpergehalt (Volumen)
~ 97 %
Shore D Härte
~ 77 (3 Tage / +23°C) | (DIN 53505) |
Abriebfestigkeit
100 mg* (CS 10/1000/1000) (7 Tage / +23°C) | (DIN 53109 (Taber Abraser Test)) |
*Werte wurden bestimmt mit Quarzsand F 34 (0,1 - 0,3 mm) der Quarzwerke GmbH Frechen
Druckfestigkeit
Harz: ~ 80 N/mm² (gefüllt 1:0,3 mit F34*) (28 Tage / +23°C) | (EN 196-1) |
Biegezugfestigkeit
Harz: ~ 40 N/mm² (gefüllt 1:0,3 mit F34*) (28 Tage / +23°C) | (EN 196-1) |
Haftzugfestigkeit
> 1,5 N/mm² (Betonbruch) | (ISO 4624) |
Elektrostatisches Verhalten
Erdableitwiderstand1) | Rg < 109 Ω |
Durchschnittlicher Widerstand2) | Rg ≤ 106 Ω |
1) Dieses Produkt erfüllt die Anforderungen der ATEX 137
2) Werte werden durch Umgebungsbedingungen (z.B. Temperatur und Feuchtigkeit) und Messgeräte beeinflusst.
Thermische Beständigkeit
Belastung* | trockene Hitze |
permanent | +50°C |
kurzzeitig max. 7 Tage | +80°C |
kurzzeitig max. 2 Stunden | +100°C |
Kurzzeitig trockene und nasse Hitze bis +80°C ohne gleichzeitige chemische Belastung (z.B. Dampfreinigung).
Chemische Beständigkeit
Siehe Chemikalienbeständigkeitsliste.
Anwendung
Mischverhältnis
Komponente A : Komponente B = 84 : 16 Gewichtsteile
Lufttemperatur
mindestens +10°C / maximal +30°C
Relative Luftfeuchtigkeit
maximal 80 % r.F.
Taupunkt
Während der Applikation und der Aushärtung muss die Untergrundtemperatur mindestens +3°C über der Taupunkttemperatur liegen. Vor Betauung schützen!
Zu beachten: niedrige Temperaturen und hohe Luftfeuchtigkeit erhöhen die Gefahr des Ausblühens.
Untergrundtemperatur
mindestens +10°C / maximal +30°C
Untergrundfeuchtigkeit
<4 % Feuchtigkeitsgehalt.
Testmethode: Sika®-Tramex, CM-Messung oder Darr-Methode. Keine aufsteigende Feuchtigkeit gemäss ASTM (Polyethylenfolie).
Topfzeit
Temperatur | Zeit |
+10°C | ~ 40 Minuten |
+20°C | ~ 25 Minuten |
+30°C | ~ 15 Minuten |
Aushärtezeit
Vor der Verarbeitung von Sikafloor®-262 AS N auf Sikafloor®-220 W Conductive:
Untergrundtemperatur | Minimum | Maximum |
+10°C | 26 Stunden | 7 Tage |
+20°C | 17 Stunden | 5 Tage |
+30°C | 12 Stunden | 4 Tage |
Die angegebenen Zeiten werden durch ändernde Bedingungen, insbesondere durch Temperatur und Luftfeuchtigkeit beeinflusst.
Appliziertes Material Einsatzbereit
Temperatur | begehbar | befahrbar | vollständig ausgehärtet |
+10°C | ~ 30 Stunden | ~ 5 Tage | ~ 10 Tage |
+20°C | ~ 24 Stunden | ~ 3 Tage | ~ 7 Tage |
+30°C | ~ 16 Stunden | ~ 2 Tage | ~ 5 Tage |
Die angegebenen Zeiten werden durch ändernde Bedingungen, insbesondere durch Temperatur und Luftfeuchtigkeit beeinflusst.
Verbrauch
Beschichtungssystem | Produkt | Verbrauch |
Selbstverlaufende Beschichtung für erhöhte optische Ansprüche (bei hellen Farbtöne) (Schichtdicke ~ 1,5 mm) | Sikafloor®-262 AS N gefüllt mit Sikafloor® Filler 1* | Maximum 2,5 kg/m² Binder + Sikafloor® Filler 1* abhängig von der Temperatur variiert der Füllgrad von 1 : 0,1 Gew.-% (2,3 + 0,2 kg/m²) bis 1 : 0,2 Gew.-% (2,1 + 0,4 kg/m²) |
Selbstverlaufende Beschichtung (Schichtdicke ~ 1,5 mm) | Sikafloor®-262 AS N gefüllt mit Quarzsand F34* | Maximum 2,5 kg/m² Binder + Quarzsand F34* abhängig von der Temperatur variiert der Füllgrad von 1 : 0,1 Gew.-% (2,3 + 0,2 kg/m²) bis 1 : 0,3 Gew.-% (1,9 + 0,6 kg/m²) |
Die Verbrauchsangaben sind rechnerische Werte und beinhalten keine Zugaben für Porosität, Untergrundrauigkeit, Niveauunterschiede, Materialverlust, etc.
*Alle Werte wurden mit Quarzsand 0,1-0,3 mm der Quarzwerke GmbH Frechen und Sikafloor® Filler 1 gemessen. Andere Quarzsande haben einen Einfluss auf das Produkt, wie z.B. Füllgrad, Verlaufseigenschaften und Ästhetik. Grundsätzlich gilt: je niedriger die Temperatur desto geringer der Füllgrad.
MISCHEN
Komponente A vor Gebrauch gut aufrühren. Die Komponenten A + B nach vorgeschriebenem Mischungsverhältnis mit einem elektrischen Rührgerät (ca. 300 - 400 U/min) intensiv mischen; ggf. die vorgesehenen Teile Quarzsand zugeben und weitere 2 Minuten mischen.
Die Mischdauer beträgt mindestens 3 Minuten und ist erst dann beendet, wenn eine homogene Mischung vorliegt. Gemischtes Material in ein sauberes Gefäß umfüllen (umtopfen) und nochmals kurz durchmischen. Das Einrühren von Luft ist zu vermeiden.
Mischwerkzeuge
Sikafloor®-262 AS N muss mit einem niedertourigen, elektrischen Mixer (300 - 400 U/min) oder anderem, geeignetem Gerät gemischt werden.
VERARBEITUNG
Sikafloor®-262 AS N wird streifenförmig aufgegossen, mit Zahnspachtel oder Zahnrakel verteilt und auf die gewünschte Schichtdicke aufgezogen. Die frisch aufgezogene Schicht muss für ein besseres Finish mit der Rückseite der Spachtel oder Rakel noch einmal glatt gezogen werden. Anschliessend (innerhalb von 10 Minuten) ist die frische Beschichtung mit der Stachelwalze im Kreuzgang (mindestens 2 Mal) intensiv zu entlüften.WERKZEUGREINIGUNG
Alle Arbeitsgeräte sofort nach Gebrauch mit Sika Verdünner C reinigen. Ausgehärtetes Material kann nur noch mechanisch entfernt werden.