Sikadur®-31+
2-komponentiger, sehr emissionsarmer Epoxidharzklebstoff
2-komponentiger, lösemittelfreier, thixotroper Epoxidharzklebstoff mit sehr geringen Emissionen, der auf diversen Baumaterialien sehr gute Haftung aufweist, auch auf mattfeuchten Untergründen. Besitzt hohe mechanische Festigkeiten und kann für statisch relevante Betonreparaturen, Fugen- und Rissverfüllungen verwendet werden.
- Einfacher Mischvorgang und Verarbeitung
- Sehr gute Haftung auf vielen Baumaterialien (auch mattfeuchte Untergründe)
- Hohe Früh- und Endfestigkeiten
- Thixotrope Konsistenz: kein Absacken bei vertikalen und über Kopf Anwendungen
- Keine Grundierung erforderlich
- Schwindfreie Aushärtung
- Undurchlässig für viele Flüssigkeiten und Wasserdampf
- Verwendung im Innen- und Aussenbereich
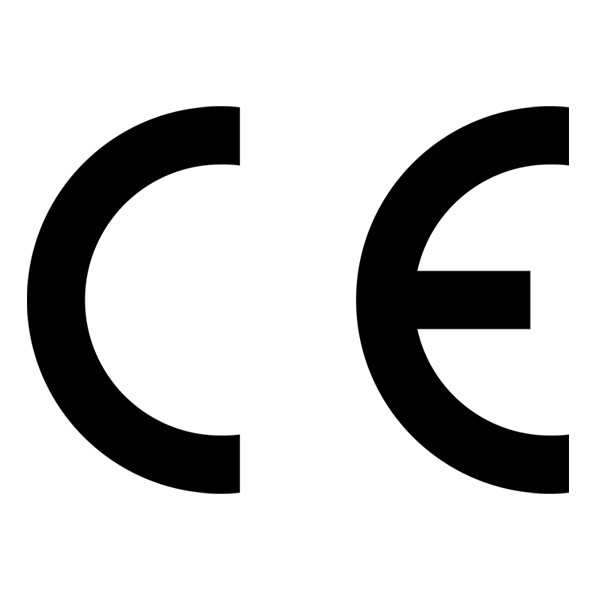
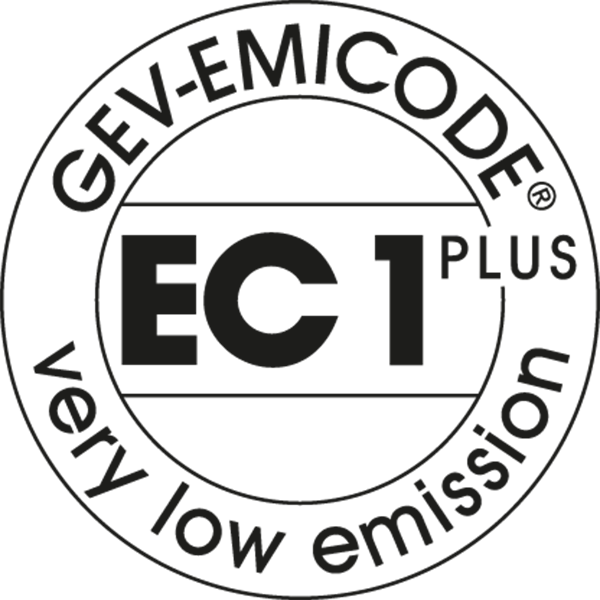